About | ECITTT | Conference Programme | Abstracts (6.)
EFFICIENT TOOLS FOR DETAILED MODELLING AND ANALYSIS OF WELDED
PRESSURE VESSEL JOINTS ACCORDING TO LOCAL FATIGUE APPROACHES
Jürgen Rudolph, Eckart Weiß and Michael Forster
University of Dortmund
Germany
http://www.chemietechnik.uni-dortmund.de/cab/cab.html
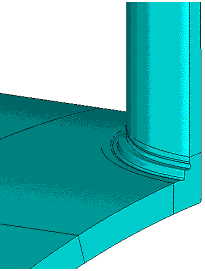
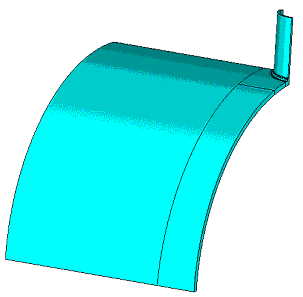
Figure 1: Nozzle-to-vessel intersection
Pressure vessel components are frequently submitted to various kinds of cyclic mechanical and thermomechanical loadings. Particularly, welded joints are susceptible to possible fatigue damage. Currently, design by analysis is based on one or several of the following concepts for welded parts:
- Nominal stress approach,
- Structural stress approach,
- Notch stress approach,
- Local strain approach and
- Crack propagation approach.
Practical considerations imply a clear trend towards local approaches based on structural stresses, notch stresses or local strains. The applicability of these concepts to particular welded components under certain operating conditions mainly depend on:
- Quality requirements of pressure vessel weld seams according to design codes,
- Availability of experimental data bases for statistically safe fatigue curves,
- Clear definition of the failure criterion (e.g. technical crack initiation and fracture) and
- Existence of high plastic deformations (Low Cycle Fatigue = LCF).
Current implementations of structural and notch stress approaches are used for life assessment of sharply notched welded joints of lower manufacturing quality in the as welded condition and with inherent defects (failure criterion fracture, characteristic slope of m=3 of fatigue curves). Alternatively, a linear elastic fracture mechanics approach is possible in these cases. Quality standards are particularly high for cyclically loaded pressure vessel weld seams in the context of safety considerations within a fail-safe design strategy and especially under low cycle loading conditions. Postwelding operations such as weld toe grinding or TIG and plasma dressing are useful methods for significant improvements of fatigue life. The design approach of these high quality weld seams should be based on local strains (failure criterion technical crack initiation).
All the design approaches mentioned require appropriate CAD-models of the weld seam as the basis of numerical analysis (FEM, BEM) as one important module of life assessment. The development of quantitative and qualitative guidelines for modelling and meshing has to be considered as one important task of research activities. Detailed and fully parameterised models based on these guidelines should be offered for practical application in engineering design within a consecutive phase. Thus, the quality and reproducibility of analysis results can be ensured.
Recently, a general strategy for the appropriate description of the macroscopic geometry of weld seams has been developed for application within the structural, notch stress and local strain approaches. It is generally based on an simple adaptive nominal weld seam as used in technical drawings. A minimum set of geometry parameters is used to derive the detailed model of the weld seam as required within the applied design approach. The strategy is derived for plane models and then transferred to more complicated 3D-structures by the application of plane sections.
Modelling requirements are significantly different within the design approaches mentioned. They range from simple models for structural stress analysis to complicated and realistic 3D-descriptions of special weld seam geometries within the local strain approach. It will be shown that a large set of welded pressure vessel components (including common imperfections such as axial or angular misalignment) of high practical importance can be integrated in this design approach. They range from relatively simple 2D butt welded details to complicated structural details such as nozzle-to-vessel intersections (see figure 1) and T-joints. Application of the local strain approach directly supports comparative design with respect to fatigue behaviour and the consideration of the improvement of weld seam quality within the design approach.
The modelling strategy presented here needs to be combined with appropriate qualitative and quantitative guidelines for FE- and BE-meshing. Thus, the development of specialized software tools for highly automated and effective practical use is possible and necessary. Models of complicated 3D-structures should preferably be generated within specialized CAD-systems and then transferred to the FE- or BE-preprocessor for meshing and numerical analysis. In this context, the availability of special repair tools with efficient automated and interactive features is extremely important for the reduction of cost and lead time. Smooth data transfer capabilities can be considered as one partial module within a modelling and numerical analysis chain for fatigue life assessment.
One current project of cooperation between Dortmund University and Fluxus Technology Ltd, Suffolk, UK is aimed at the development of highly automated and parametric tools for direct practical application within local approaches of fatigue analysis for pressure vessel components.